You have a technical problem with one of our products? Here’s how you should go forward …
Support
We provide support from Monday to Thursday from 8:00 am to 5:00 pm, Friday from 8:00 am to 3:30 pm (it's currently 03:01 (3:01 am) in Switzerland (GMT+2)).
-
lacquer-coating
- Check
condition ofsynthetic roller. Ensure thatapplication surface is smooth and does not show any defects > replace if required
- Measure velocity of overhead conveyor at welder for reference purposes. Set speed of outside lacquering unit equal to conveyor or alternatively, set it slightly higher (2 – 3 % above effective conveyor speed) > verify speed setting by measuring exact velocity, picking up speed of application surface at synthetic roller
- Apply slightly more lacquer on
outer side seam. Please follow point 7.2 (Adjustment of the lacquer quantity) in the provided instruction manual for the ORC.
- As a last precaution, check the viscosity of your lacquer by using the DIN 4 cup supplied. Recommended viscosity: 20 – 25 seconds. Depending on type of lacquer used, add corresponding thinner / water in order to achieve required viscosity.
- Check
-
conveyor curing essentials powder-coating-unit-cpc-1
FREI AG white:
– RAL 7035FREI AG blue:
– RAL 5017 -
essentials
Attached PDF contains all information you are looking for!
-
curing lacquer-coating
Correctives 1 – Too much heat during the first part of the curing process:
1.1. The tin flow has to to be only as wide as the width of the powder and / or lacquer stripe and not more (usually around 15 mm for food and aerosol cans)!
– This width also covers lateral shifting can bodies during daily production!
– The internal powder must have a low melting point, starting from about 180° C!
– Most commercially available and good powder coats are fulfilling this demand. For further information for recommended powders, please contact our support.1.2. The conveyor speed in the oven is too high, therefore the curing time is too short!
– Distances between the cans of more than 1/2 canbody height is a reduction in curing time of 25% (or from 5 sec. to only about 3,8 sec.!)1.3. The adjustment of the coil to the can bodies is wrong.
1.4. The curing length is too short (before ordering a longer curing system, please first follow the Correctives 2 and 3!)
Corrective 2 – The wet lacquer application is not constant, too thick or too thin!
2.1. Especially for induction curing system, with shorter curing time, a constant film thickness is required!
– Please note that a constant and a “as thin as possible” lacquer application is essential not only on the curing effect, but it also reduces the lacquer cost!2.2. The can body must be round – within standard tolerance, overlap beginning and end must be equal!
2.3. Depending on the configuration, rubber roller or steel rollers must be used!
– For further information and / or support contact our support.2.4. The speed of the application roller is wrong, compared to the passing can bodies!
– Generally, too high application roll speed leads to worse results than a too slow one.
– Depending on steel or rubber rollers different speed than can body speed might be used, but must be controlled and monitored.2.5. The material and / or the form of the rubber/steel roller profile is wrong!
– For the use of a steel roll (longer lifetime) we urgently recommend to have a “supporting conveyor “under” can body (contact our support)Corrective 3 – Wrong wet lacquer type in use:
3.1. Not every wet lacquer type is applicable for induction curing system due to the fact that the heat up ramps are much faster than with a gas curing system
– For a list of recommended (and pricewise competitive!) lacquers contact our support.3.2. The correct viscosity and therefore the proportion of solvent is most important for a non-porous side seam protection.
Problem not yet solved?
We are happy to assist you!
For any technical support please contact Beat Pfändler.
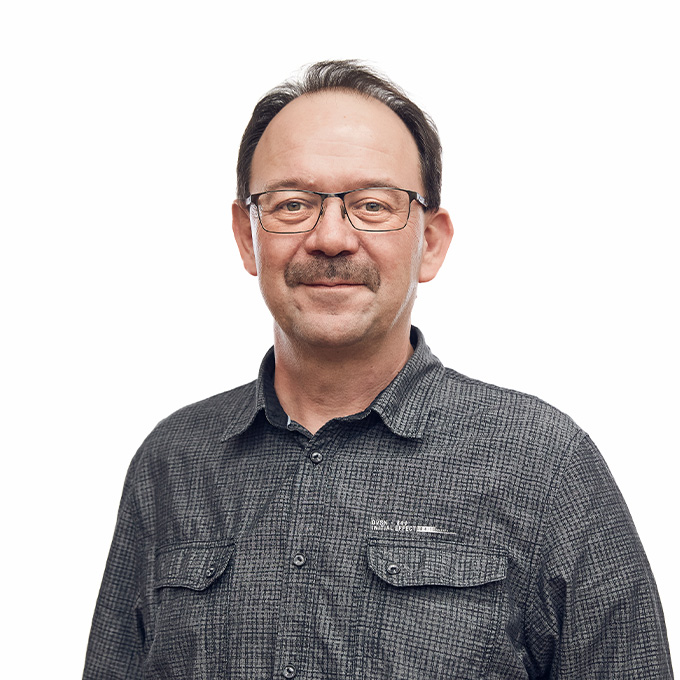